Analysis of the Wear Failure of Cone Crusher Liner at Copper Mine
In view of the work conditions of Copper Mine, the analysis of the wear failure of the cone crusher was made. SEM analysis showed that drilling, cutting and squeezing (impacting) of ore which resulted in pits were the dominating wear means and the fatigue spalling caused by low-frequency fatigue was one of the wear failure means. Therefore, the liner materials should be required to have both very high surface to resist the drilling and cutting of ore and very high strength and toughness to resist low-frequency fatigue and impact load. So, high manganese steel alloying was selected to increase the preliminary hardness and work hardening rate of the liner. Meanwhile, the improvement of metallurgy foundry and heat treatment qualities of high manganese steel was also a factor that couldn’t be ignored.
Our customer, Dexing copper mine, which is the largest copper mine in Asia. It has more than 30 sets cone crushers, so need a large number of cone crushers wear parts every year. It has many crusher wear parts suppliers, however, the quality of these parts is not stable. Therefore, our foundry had helped it to find the wear failure of cone crusher liners and improve its span life.
Working Condition
The ore in the Dexing Copper Mine can be divided into porphyry and phyllite-type ore according to the type of ore body rock. The ratio of ore volume is 1: 3. In the mining area, there are three industrial types of oxidized ore, mixed ore, and primary sulfide ore. The sulfide ore is the main type and accounts for more than 99% of the mass.
The hardness of Dexing copper ore is generally between f = 5-8, which belongs to medium-hard ore. The average compressive strength of the phyllite type ore is 84.8 MPa, and the average compressive strength of the granodiorite-type ore is 109.2 MPa.
Sampling
The key step of wear failure analysis is to analyze the morphology of the wear surface, so the sample must be taken from the fresh wear surface of the wear debris. The moving cone (liner) we sampled was just removed from the cone crusher and shipped back in time.
The broken cone crusher liner is cut into large samples by oxygen-acetylene flame, and 4 samples are taken from top to bottom. The size of the sample should be such that the sampling site is not affected by heat. Then, through the wire cutting process, take out the sample at the center of the large sample for scanning electron microscope to observe the wear morphology. The size of the sample is about 10 mm × 10 mm × 10 mm, and one sample is taken to measure the change in microhardness from the surface inward.
Observation of the specimen was performed on an S-2700 scanning electron microscope. Before observation by the electron microscope, the samples were cleaned with ultrasonic waves.
Wear Morphology and Wear Mechanism
The three-body abrasive wear is formed between the cone crusher mantle, cone crusher concave and the ground ore, and the surface of the liner is in a complex stress state.
Under the action of huge spring compressive stress, the ore generates huge compressive stress on the local surface of the lining plate, and at the same time, the moving cone generates high shear stress at the same time. The two acts at the same time, which causes chiseling, cutting and extrusion of the lining plate.

Wear Morphology After Cone Crusher Liners Failure x100
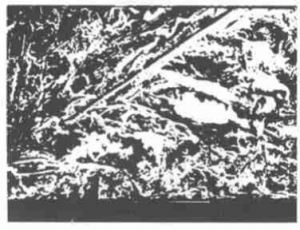
Wear Morphology After Cone Crusher Liners Failure x500
From the first picture “Wear Morphology After Cone Crusher Liners Failure x100”, The cone-crushing motorized lining plate performs an eccentric rotation motion. When it is deflected to the fixed lining plate, it will give a huge impact load to the broken ore, causing the lining plate to be squeezed and plastically deformed. In the case of repeated repeated plastic deformation, the liner forms numerous squeeze (impact) pits, check the “Wear Morphology After Cone Crusher Liners Failure x500”.
At the same time, the ore-bearing the huge load will subject the lining plate to compression stress and shear stress. The compression stress causes plastic deformation of the moving liner. In the case of repeated repeated plastic deformation, numerous squeezing (impact) pits are formed on the surface of the liner, like the following “Squeeze (impact) pits on the wearing surface of the cone crusher liner” pictures. At the same time, at the bottom of the extrusion pit, after repeated extrusion, deformation strengthening occurs and plasticity is exhausted to form a brittle fracture. Its appearance “Morphology of brittle fracture at the bottom of the pit”
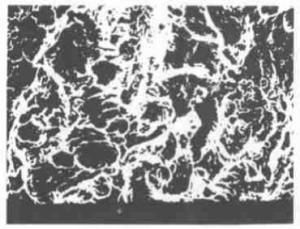
Squeeze (impact) pits on the wearing surface of the cone crusher liner
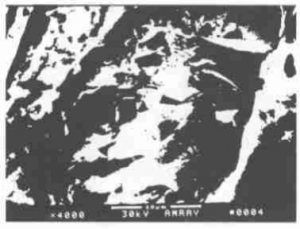
Morphology of brittle fracture at the bottom of the pit
Further observations revealed that the ore squeezed the surface of the liner under the effect of huge crushing stress. Because the ore has a low Platts hardness f value, the f value actually reflects the compressive strength of the ore, f=R/100, R means Compressive strength. Therefore, the compressive strength of the ore is low, the breaking strength is also low, and it is easy to break. After the ore breaks, it is squeezed to the bottom of the pit due to the lower hardness of the lining, see the following picture:
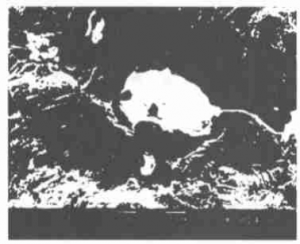
The ore was embedded in the bottom of the pit and cracked at the edge of the pit x300
At the same time, as the moving cone rotates, shear stress is generated between the ore and the liner. The sliding ore and the ore squeezed at the bottom of the pit cut and cut the surface of the lining.
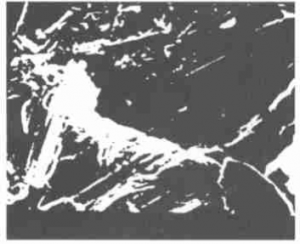
The surface of the liner is chiseled and cut by ore x800
Therefore, in the actual operation of the cone crusher lining, there are simultaneously cutting, cutting and pressing (impact) pits Various forms of wear. As for the proportion of the three types of wear, it is not only related to the force and size of the ore, but also to the value of the Platts hardness f that reflects the compressive strength of the ore.
It should be pointed out that the cone crusher has a large crushing force and a high rotation speed. Under the action of huge compression and shear pressure, the lining board is subjected to periodic contact fatigue loads. Fatigue cracks can easily occur on the subsurface layer, resulting in fatigue spalling. Flaking is also one of the failure factors of the wear of the crusher liner.
In summary, the wear mechanism of the cone crusher lining is the coexistence of cutting wear, plastic wear and fatigue wear. With the different working conditions, especially the different F value of the hardness of the ore, the proportions of the three wear mechanisms are different.
Cone Crusher Liner surface hardening
Because the material of the sampled cone crusher liner (lining plate) is high manganese steel, the lining plate is subjected to a huge impact load during the operation of the cone crusher, so that it has a good work hardening effect.
Cone Crusher Liner Hardness
Item | Distance From Surface (mm) | |||||||||
0 | 0.5 | 1.0 | 1.5 | 2.0 | 3.0 | 4.0 | 6.0 | 7.0 | 8.0 | |
1 (upper area) | 527 | 350 | 336 | 313 | 291 | 285 | 285 | 250 | 245 | 264 |
2(middle area) | 569 | 336 | 283 | 299 | 265 | 248 | 257 | 243 | 245 | 245 |
3(lower area) | 494 | 289 | 280 | 272 | 274 | 274 | 269 | 246 | 245 | 230 |
It can be seen from the table test results that the cone crusher liner is subjected to a huge impact load in the crushed ore. The hardness Hv of the liner surface can be as high as 500 or more, but the hardening depth is only within 2 mm.
Therefore, the liner is required to have good toughness and sufficient strength to resist the huge impact load and cause chipping.
The surface hardening values of different parts of the same lining board are different, which shows that different parts of the lining board have different stresses and different sizes of ore.
The upper part of the moving lining board is impacted by a large ore, so the hardening value is the highest; while in the lower part of the moving lining board, the ore has been broken, and its surface hardening value is low.
Selection Of Materials
According to the above analysis of wear morphology and wear mechanism, the cone crusher lining not only requires high surface hardness to resist ore chiseling and cutting but also requires high strength and toughness to improve resistance to huge impact loads and Low cycle fatigue ability, will not break and break. Therefore, the basic requirement for the material selection of the cone crusher liner is to increase the surface hardness as much as possible and to improve its resistance to cutting wear while ensuring that the liner does not crack. Due to the high plasticity and toughness of high manganese steel, and the unmatched high work hardening ability of other wear-resistant materials, high manganese steel is still the material of choice for cone crusher linings. However, as the power of the crusher continues to increase, the crushing ratio increases and the ore grade continues to decrease, especially the Dexing Copper Mine is a lean ore, and it is generally difficult for high manganese steel to meet production requirements. Therefore, it is necessary to increase the initial hardness of the high-manganese steel and increase its work hardening rate under the premise of better exerting the inherent characteristics of the high-manganese steel and ensuring that the high-manganese steel has proper plasticity and toughness. Based on this, based on the composition of ordinary high manganese steel, we consider alloying treatment to improve the strength and hardness of high manganese steel and evenly distribute a considerable number of high hardness mass points on the basis of austenite to improve the worn form of the liner, Slow down the rate of wear. However, the addition of alloying elements to high-manganese steels is beneficial to the improvement of strength and hardness, but it will inevitably lead to the reduction of plasticity and toughness. Therefore, the amount of alloying elements must be added in order to avoid excessive reduction of plasticity and toughness and lead to fragmentation. So our foundry suggest using CrMoVTiRe manganese steel to cast their cone crusher liners,
CrMoVTiRe Manganese Steel Chemical Composition | |||||||||
C | Si | Mn | S | P | Cr | Mo | V | Ti | Re |
1. 3~ 1. 5 | 0. 3~ 0. 6 | 13~ 15 | < 0. 04 | < 0. 07 | 1. 8~ 2. 2 | 0. 8~ 1. 2 | 0. 3~ 0. 5 | 0. 15~ 0. 25 | 0. 5 |
The test results show that the initial hardness of CrMoV TiRe high manganese steel can reach about HB 260, which is conducive to improving the resistance to cutting wear.
However, the addition of alloying elements, especially the addition of carbide-forming elements, will inevitably lead to an increase in the number of undissolved carbides, which will reduce the plasticity and toughness to a certain extent compared with ordinary high-manganese steels.
While attaching importance to the alloying of high-manganese steels, we must not neglect the improvement of metallurgical quality, especially reducing the amount of phosphorus and inclusions. This is an economical and convenient way to improve the service life of high-manganese steel linings. During water toughness treatment, heat treatment process parameters such as water toughness treatment temperature, water inlet and outlet time, and water temperature should be strictly controlled so that the amount of undissolved carbides and precipitated carbides is controlled within the range prescribed by national standards.
It should be pointed out that while paying attention to the material of the cone crusher liner, the formulation of the casting process should not be ignored. The wall thickness of the cone crusher lining is large, and the maximum wall thickness of the fine crushed lining can reach 200 mm.If ordinary sand casting is used, the cooling rate is slower, and the casting temperature is not strictly controlled. Coarse. Due to the coarse grains, only one grain is observed when zoomed in to 100 times, so it is only zoomed in to 50 times, so it cannot be evaluated according to the national standard of GB6394. Grain refinement will help to increase the service life of the liner.
Therefore, in the casting process, it is recommended to use metal mold sand and reduce the pouring temperature, which will help refine the grain of high manganese steel lining plate.