Crush different materials need different cone crusher cavities. The suitable cavities will help you get more profit and crush more material. Normally, there are six kinds of cone crusher mantles and concaves types:
- Standard
- Medium
- Fine
- Coarse
- Extra Coarse
- Extra Fine
A wide range of liners are available to accommodate coarse and fine feeds, but which you choose depends on several factors. The most important factor in Cone Crusher liner selection is the feed.
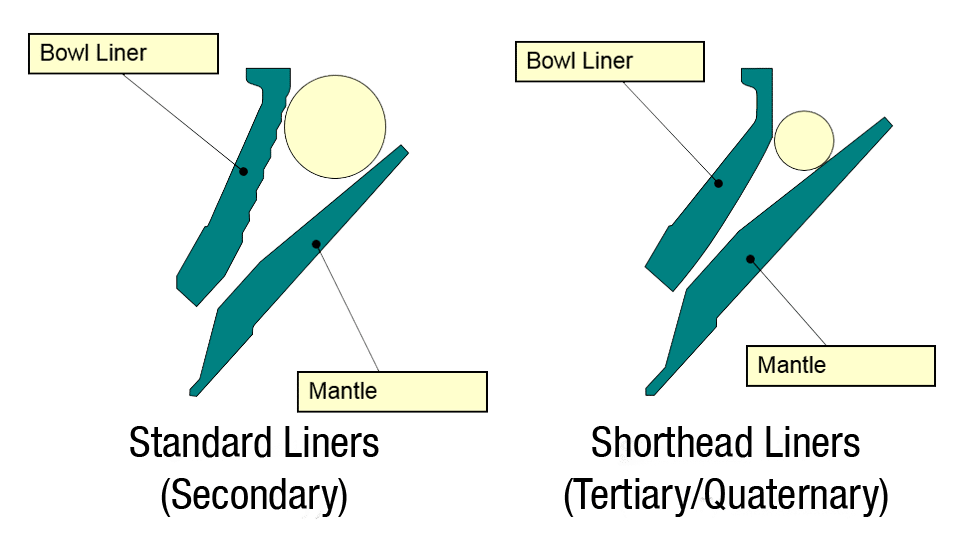
Cone Crusher Cavity Types
You should have a well-graded feed going into the crushing chamber. A well-graded feed is generally considered as:
- 90-100% passing the closed-side feed opening. Some people look at 80% of the open side as well and select the smaller of the two.
- 40-60% passing the midpoint.
- 0-10% passing the closed-side setting.
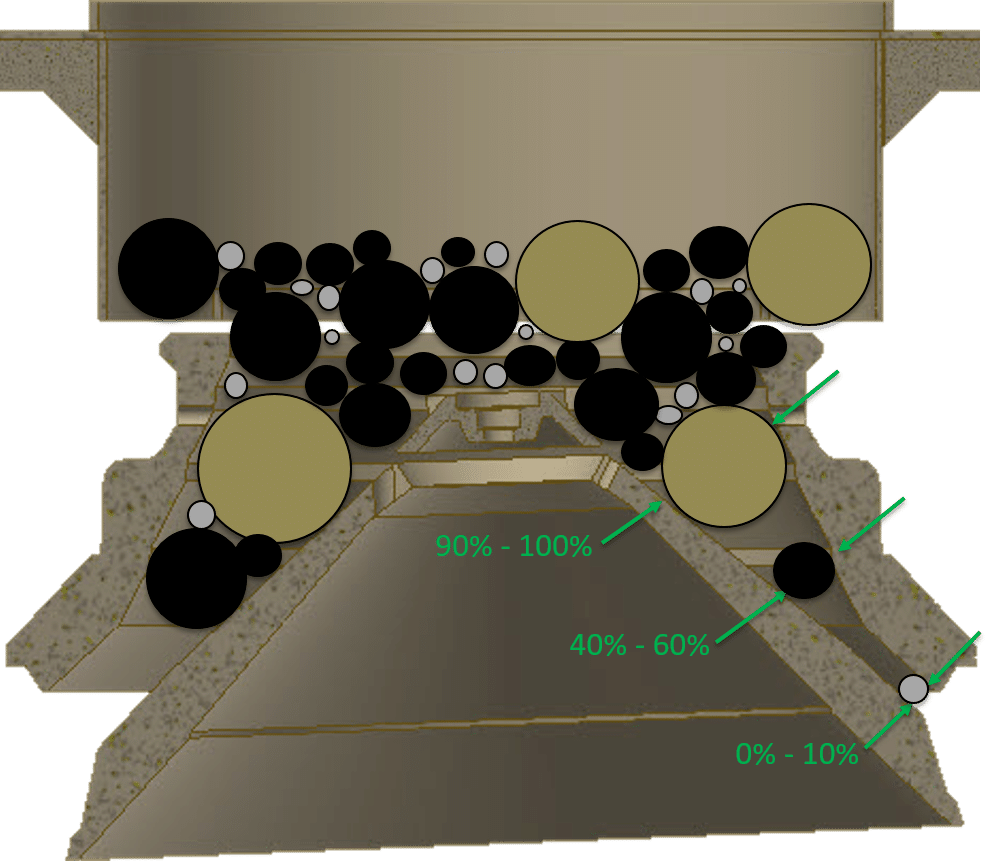
A well-graded feed to the Cone Crusher.
You want to match the entire feed gradation, not just the feed size so that you utilize the entire chamber. It is important to utilize as much of the crushing chamber as possible to get the required reduction and desired throughput.
Plant feed size and the output from your previous crushing stage define your top feed size, which will give the maximum cavity opening. The cavity opening should not be too big in relation to the top feed size. Cavity openings that are much larger than the feed size lead to poorly utilized reduction and liners.
If the feed size is too small, the majority of the crushing takes place in the lowest portion of the cavity, which means the bottom of the liners will wear away faster than the top of the liners. The production will decrease due to the poor reduction ratio. The power limit of the crusher will be exceeded at a minimal volume level, and you’ll run the risk of improper bearing alignment.
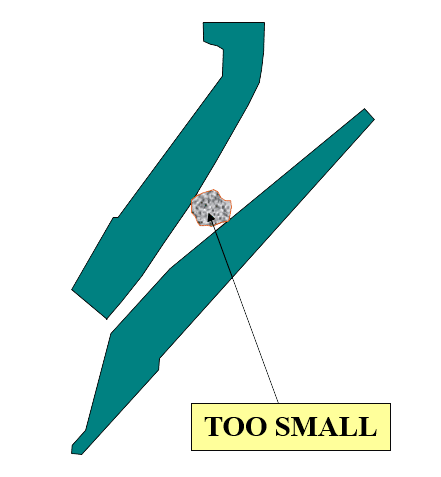
Cone feed too small for cone crusher liner
Most of the wear on crusher liners occurs right before the parallel zone (the smallest space between the mantle and the concaves where the final crushing takes place), but this wear will be accentuated if the feed is too small, and you’ll end up with a bowled-out pocket before the parallel zone way too soon.
On the other hand, if the feed size is too coarse, the feed material will keep percolating around the feed opening, causing the top of the liners to wear away faster. Because the feed opening is bridged over, throughput is reduced and production decreases. The output gradation will be coarser, and the product will be slabby, not cubical. The volume limit will be exceeded at a minimal power draw.
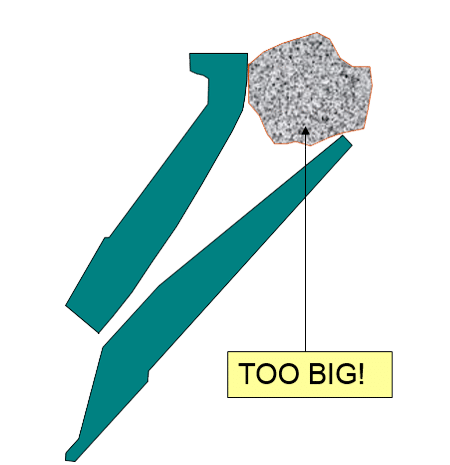
Cone feed too big for cone crusher liner
Understanding your gradation going into the crusher helps you to choose the right liner configuration necessary to achieve your production goals. The right liner selection gives you a better nip and more room to adjust other parameters, such as the closed-side setting.
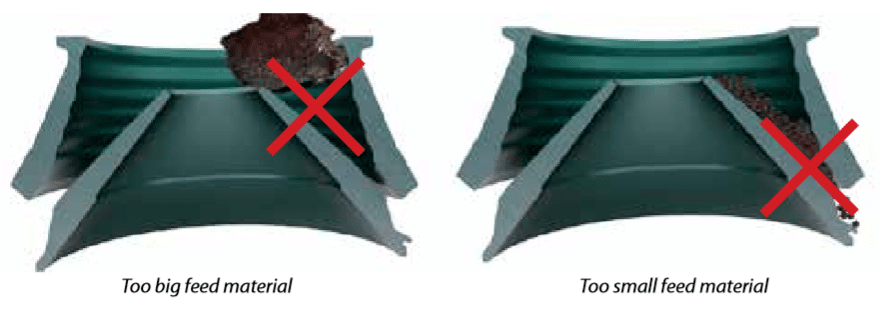
Cone Crusher incorrect feed