Abrasion analysis and optimization design of cone crusher liners in hydraulic cone crusher
Cone crusher cavity and cone crusher liners material are the most major factors affecting the abrasion of the concave and mantle in the hydraulic cone crusher. We have a customer, who runs KP100 hydraulic cone crusher to crush cobblestone. Each set of cone crusher liners can crush 5400 tons and work 600 hours. Based on its working conditions, we will analyze the cone crusher liner abrasion and optimization design the liners.
The cone crusher liners of the cone crusher are both important parts and major wearing parts. A pair of well-designed and well-made liners can not only ensure the production efficiency of the crusher, but also save energy, labor, and raw materials, and ensure product quality. There are many factors that affect the wear of the liner, such as material hardness, particle size, moisture, yield and feeding method, etc., but the more important are the cavity curve design and material selection factors.
Cone Crusher Liner Abrasion Analysis
Based on our customer KP100 cone crusher working conditions:
- 1 set of cone crusher liner
- Crush material: cobblestone
- Working life: 600 hours
- Crushed 5400 tons in total
The curve of the cone crusher mantle and concave after mapping wear is shown in the following figure:

Abrasion of Cone Crusher Mantle
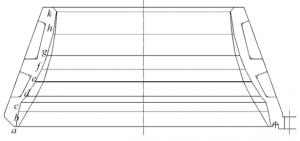
Abrasion of Cone Crusher Concave
The wear amount of each section along the direction of the height of the concave and mantle are listed in the table:
Lable | Cone Crusher Mantle | Cone Crusher Concave | ||
Height | Abrasion amount | Height | Abrasion amount | |
a | 0 | 8 | 0 | 13.5 |
b | 50 | 29 | 50 | 15 |
c | 80 | 39 | 83 | 36.5 |
d | 101 | 33 | 110 | 36.5 |
e | 149 | 27.8 | 144 | 32.5 |
f | 190 | 19 | 193 | 20 |
g | 236 | 14.5 | 247 | 13 |
h | 307 | 6.3 | 350 | 1 |
k | 382 | 2.5 | 415 | 1 |
Taking the height of the concave and mantle as the abscissa and the wear amount of each section as the ordinate, the wear and tear curves of the concave and mantle are respectively made as shown in the figure.
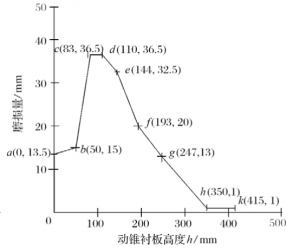
Abrasion curve of cone crusher concave
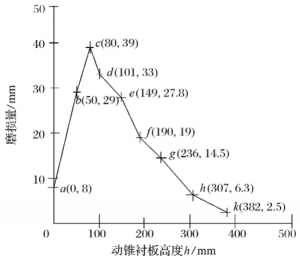
Abrasion curve of cone crusher mantle
Wear analysis of cone crusher mantle
Based on the above figures, the amount of wear at different positions of the cone crusher mantle is different.
From point k to point d, there is a gradual wear section, that is, the wear amount of the cone crusher mantle curve gradually increases from point k to d at the top. Due to the point k around the upper end of this section, the cone crusher bears The huge impact load of large ore makes it have a good surface impact hardening effect (material is high manganese steel), so that the hardness of the surface of the lining board can be as high as 500 HBW, so the upper-end hardness value is the highest.
Below point k to point d, as large pieces of ore are gradually broken into medium and even small pieces, and finally broken into the required block size of the product, the impact load on the surface of the lining plate is gradually reduced, so the degree of surface impact hardening is increasing In addition, the lower volume of the cavity is smaller than the upper volume, and the same amount of material is broken, and the lower part has greater wear than the upper part. Therefore, the wear curve changes approximately linearly from point k to point d, that is, the amount of wear at point k is the smallest and point d is the largest.
From point d to point a, it is a cavity-type parallel section, and it is also a non-gradually worn section. In this section, with the gradual abrasion of the surface of the moving and fixed cone lining during the production process, the gap between the discharge openings also increases. This causes the tail cone of the moving cone to enter the cavity after the wear of the fixed cone, and finally makes the part of the tail cone and the wear curve of the fixed cone form new discharge ports and parallel regions.It is shown as the following picture:
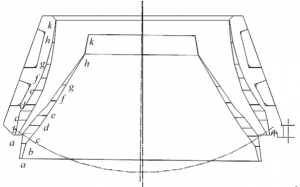
Chamber figure after abrasion
Wear analysis of cone crusher concave
Based on the above figures, the amount of wear at different positions of the cone crusher concave also is different.
From k to h, it is the inlet section. The curve of the liner in this section is approximately vertical (the moving and fixed cone curves are approximately parallel). Therefore, during the upward adjustment of the moving cone (lifetime), the inlet size and inlet The particle size of the material is basically unchanged, the impact load is balanced, and the surface impact hardening degree is basically the same, so the wear amount in this section does not change much.
The section from point h to point c is a gradual wear section, which is roughly the same as the above analysis of the fixed cone liner from point k to point d. That is, the upper point h is subjected to a large impact load from a large ore. The highest value is from point h to point c. As the impact load gradually decreases, the degree of surface impact hardening also decreases. In addition, the cavity gap decreases from top to bottom, so the wear amount is the smallest at point h. , C point is the largest, and in this section, the wear curve shows an approximately linear trend.
The section from point c to point a (that is, the tail cone section) is a non-gradual wear section. In this section, with the gradual wear of the surface of the moving and fixed cone liners, the gap between the discharge openings also continues to increase. In order to ensure product quality, the moving cone must be adjusted in the direction so that the tail cone of the moving cone gradually enters the fixed cone. In the cavity, the worn and fixed cone curves form a new crushing cavity pattern again and again until the tail of the moving cone and the worn cone curve form a new parallel zone and discharge port size.
The real wear situation of cone crusher concave and mantle
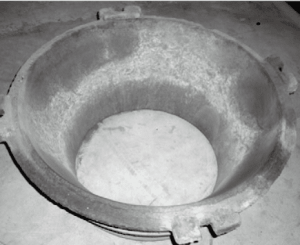
The real wear situation of cone crusher mantle (Whole)
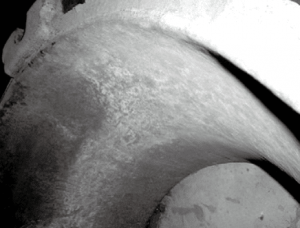
The real wear situation of cone crusher mantle (part)
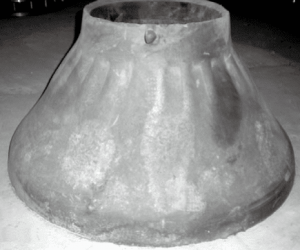
The real wear situation of cone crusher concave (whole)
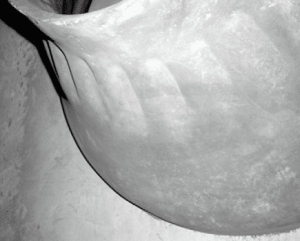
The real wear situation of cone crusher concave (part)
The result
- The cone crusher concave and mantle have basically the same amount of wear at the same height, the service life is about the same, and the cavity curve design is more reasonable.
- In the cavity-shaped parallel section, the amount of wear is much larger than the upper part. The most severe wear is the entrance of the fixed cone parallel zone, that is, the point d and below and the moving cone liner discharge port and above to point E.
- Within the limit of liner wear, although the original curve no longer exists, due to the consistent wear of the moving and fixed cone liners, during the production process, with the automatic adjustment of the size of the discharge port, the new crushing cavity type is again Secondary formation, which ensures that the grain shape of the liner after wear is basically the same as the new liner.
Optimization Design and material improvement measures
Based on the above analysis, the following design and material improvement measures can be adopted:
- Reduce the thickness of the cone crusher mantle from the k-point to the g-point (11 ~ 16 mm) to adapt to the worn liner curve. This can reduce the amount of material and ensure the life of the entire liner.
- Design the depth of the concave chute to be shallower (10 mm) and deeper (17 mm), so that it matches the worn liner curve to improve the liner during wear. Card material effect.
- By alloying (adding a certain amount of Cr, Mo and trace amounts of alloying (adding a certain amount of Cr, Mo and trace amounts of alloying (adding a certain amount of Cr, Mo and trace amounts of alloying (adding a certain amount of Cr, Mo And trace alloy elements such as V and Ti) improve the fatigue resistance and wear resistance of high manganese steel, thereby improving the weakness of insufficient wear resistance of high manganese cast steel linings.