Cone crusher liners include cone crusher mantle and cone crusher concave. Based on different situations, there are different production methods in casting those cone crusher wear parts. The main production methods include sand casting, V method casting, and lost foam casting.
Cone Crusher Liners Sand Casting
1.Using ordinary sandbox to produce cone crusher liners
The pit scraper shape is adopted, and the water glass quartz sand is hardened with carbon dioxide. The process is simple and can only be produced in small batches. At present, it is only produced in small factories and when a small number of special shaped pieces are needed.
Water glass quartz sand is used for carbon dioxide hardening. Generally, the cone crusher liners are rolled with bottom box, middle box, cover box and three boxes. The production process is relatively complicated and the amount of sand used is large. The process operation is troublesome and the dimensional accuracy is poor. The production process in below:
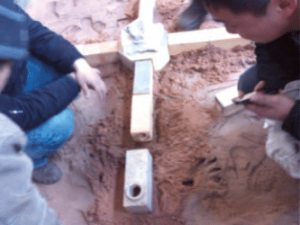
Press the gate
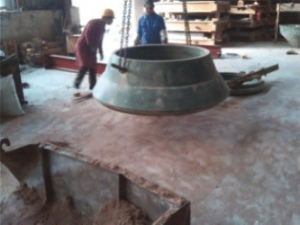
Put a wooden mold
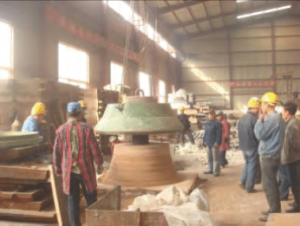
Take out wooden mold
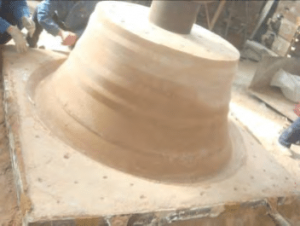
Cone crusher mantle core
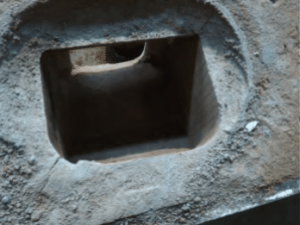
Riser neck in sand mould
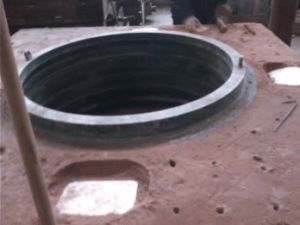
Mold to be lifted
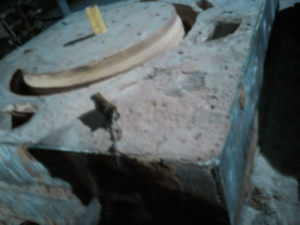
Pressed sand core
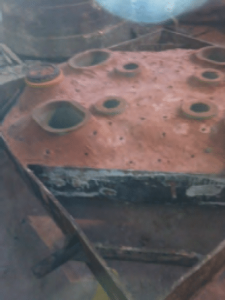
Cover box with rolled cone crusher mantle
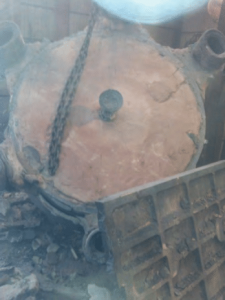
cone crusher mantle after casting

cone crusher mantle in unpacking
This production method can guarantee the quality of rolling wall castings, but the production process is complicated, the amount of sand used is large, the process is troublesome, the dimensional accuracy is poor, and the production efficiency is low.
2.Using special sandbox to produce cone crusher liners
According to the shape of the cone crusher mantle and cone crusher concave, a suitable molding sandbox is made, and water glass quartz sand is used for carbon dioxide hardening or resin sand.

Water glass upper sandbox-1
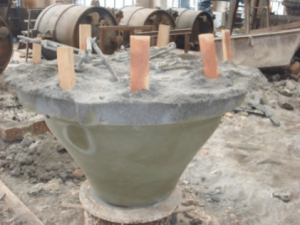
Water glass upper sandbox-2
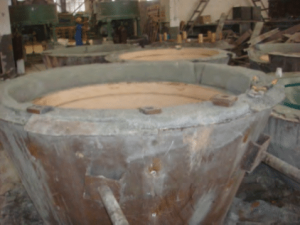
Water glass down sandbox-1
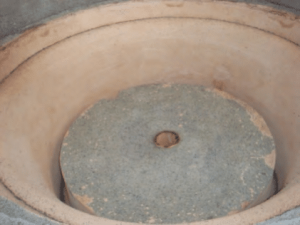
Water glass down sandbox-2
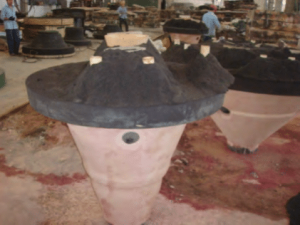
Resin sand upper sandbox
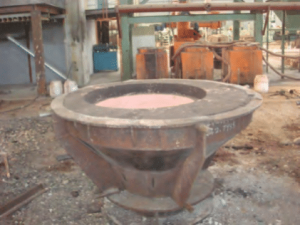
Resin sand down sandbox
The cone crusher liners using the molding sandbox has a simple production process, less sand consumption, convenient operation, and high production efficiency. It is just time-consuming and labor-intensive to make the molding flask and process equipment.
3.Production of cone crusher liners by using metal iron mold sand covering process
Production of cone crusher liners by using metal iron mold sand covering process. its production process as following pictures:
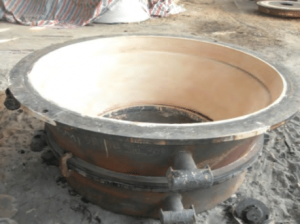
Cone crusher concave down sandbox
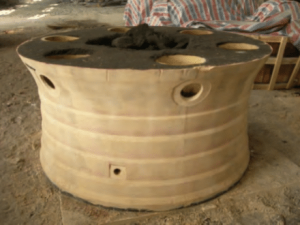
Cone crusher concave down sandbox core
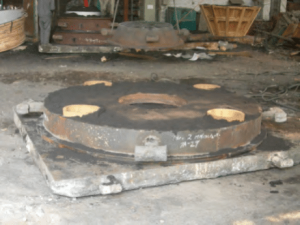
Cone crusher concave upper sandbox
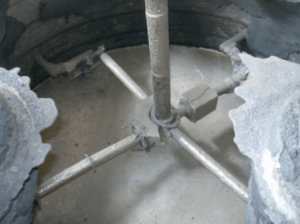
Gating system
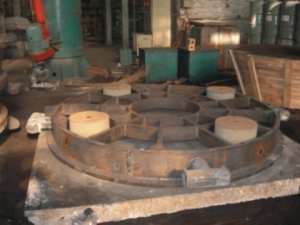
Closed box mould
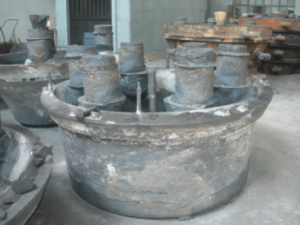
Cone crusher concave after casting
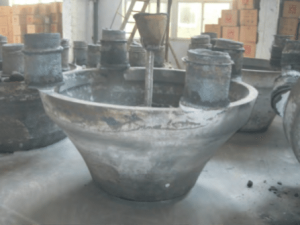
Cone crusher mantle after casting
The production of cone crusher liners by adopting metal-type iron mold sand-covering is safe and reliable, and the amount of sand used is small. Convenient operation and high production efficiency, especially to make the poured metal cool down fast, refine grains, improve the comprehensive properties such as hardness and toughness, and improve the wear resistance and service life of castings.
Cone crusher liners V method casting
The principle of V method casting is to use a plastic film to seal the sandbox, and use a vacuum pump to extract the air inside the mold, forming a pressure difference between the inside and outside of the mold. A physical modeling method to compact dry sand to form the required cavity. No binder, water, and additives are added to the molding sand, which reduces the sand processing work, and the labor for molding and casting sand cleaning is greatly reduced; the reuse rate of used sand can reach more than 95%, which achieves energy-saving and emission-reduction green casting.
For example:
The casting weight 2100 kg and has an overall dimension of 2300 mm. The key to the V method casting process is to place about 30 pieces of cold iron in the inner ring of the skirt of the cast wall, as shown in the figure. In order to increase the density of the working surface of the inner ring, the grain size of the inner ring can reach 4 or more.
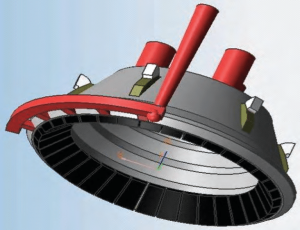
Cold iron process drawing
Casting solidification simulation of cone crusher liners using the CAE numerical simulation technology, as shown in the figure below.
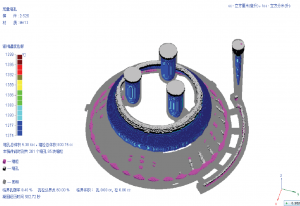
Solidification simulation drawings
Its production process as shown in the figure below:
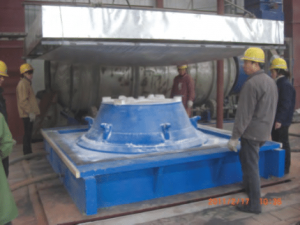
Bake plastic film for lamination
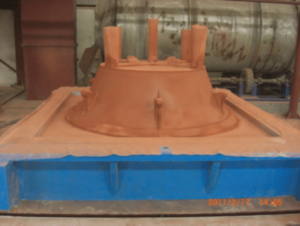
Spray V coating
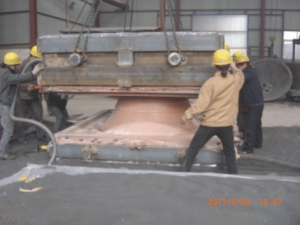
Vacuum box
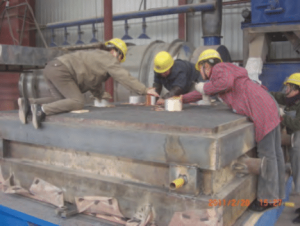
Sanding and screeding
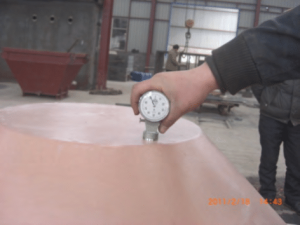
Testing the hardness of sand mold after vacuuming
V-casting technology has the following advantages:
(1) The surface of the casting is smooth and clean, the contour is clear, the dimensional accuracy is high, the dimensional tolerance can reach CT6-CT9, and the surface roughness can reach Ra = 6.3µm.
The surface quality of the casting is good.
(2) No binders and additives, no sand mixing equipment, reduced operating and maintenance costs, reduced environmental pollution, and green casting.
(3) The reuse of used sand can reach more than 95%, which solves the problem of waste sand treatment.
(4) The V method cast metal has good fluidity, strong filling ability, high metal utilization rate, high process yield, and small machining margin.
(5) The mold and the flask have a long service life, because the mold is protected by a thin film, the draft force is small, and the mold is basically not damaged.
(6) V method casting sand mold has high compactness, can be cast at low temperature, fine grains of wear-resistant castings, and good wear resistance.
Cone crusher liners lost foam casting
The lost foam casting process is:
(1) Use foam molds to produce foam patterns and pouring systems.
(2) Bond the pattern to the gating system to the mold beam module.
(3) Dip the paint on the beam module.
(4) Dry the paint.
(5) Put the module into the sandbox and fill it with dry sand.
(6) Vibration modeling makes dry sand fill the inner cavity and compact.
(7) Pouring causes the foam pattern to disappear and form a casting.
(8) After cooling, remove and clean up the castings, and use dry sand for recycling.
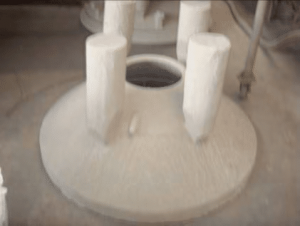
cone crusher liner lost foam casting pattern
Features of Lost Foam Production:
(1) Short production cycle and high efficiency. Because the lost pattern does not require parting, lower core, sand mixing, etc., a series of operations such as modeling and core making are omitted, and the falling sand cleaning is greatly reduced, and it is especially suitable for pouring a box of multiple pieces. Therefore, the production cycle is greatly shortened, and the efficiency can be increased by 3 to 5 times compared with ordinary sand casting.
(2) The castings have good quality and high precision. Due to dry sand, overall appearance, vacuum casting, there are no pores, slag holes, and burrs; without mold splitting, mold, and box, the dimensional accuracy of the casting can reach CT12 ~ 10, and the surface of the foamed casting is rough. The degree can reach Ra25 ~ 12.5. Therefore, the casting can be processed with little or no processing. The non-processing can keep the original surface of the casting, which saves metal and processing costs, improves wear resistance and prolongs the life of the casting.
(3) Opened up a new way for the design and manufacture of complex structure castings. Complex structural castings that are difficult to produce by ordinary casting. Originally, castings made from an assembly of several parts or multiple cores and live blocks, such as ball mill screed plates, compartment plates, etc., can be cast by foam plastic sheets after being bonded by using lost foam to make.
(4) The process is flexible and widely used. Complex parts, trial parts, repair parts, urgent parts, or a small number of castings (1 to 3 pieces) can be processed and assembled with foam boards; batches of more than 500 pieces can be formed by foaming and combined casting; regardless of the size of the casting or steel, Various alloys of iron can be made by lost foam casting.
(5) Less investment, quick results, good working conditions, and high production efficiency. Because the lost foam casting process is simple, the use of dry sand does not require sand mixing equipment and woodworking machinery, and the special sandbox is greatly reduced; the reuse rate of used sand is as high as 95%, and the amount of falling sand cleaning and the labor intensity is reduced by half.
It is easy for molders and stylists to master production technology. The reject rate is about 1%, and the process yield is more than 75%. It requires less staff, occupies less land, and has significant economic benefits.
(6) The shortcomings of the vanishing pattern are that it is easy to increase the amount of carbon, and the large plane is easy to deform.
Qiming Machinery’s Cone Crusher Liners Production Methods
Qiming machinery has all three kinds of production methods:
- We use lost foam casting to cast small parts and trail orders.
- We use V method casting to cast standard parts and OEM parts.
- We use resin sand molding to cast most of our cone crusher liners.
Choose which production method based on the real situation.