What is crusher parts– crusher parts definition
A crusher is a machine designed to reduce large rocks into smaller rocks, gravel, sand, or rock dust, which is consists of thousands of parts. These thousands of parts are called crusher parts. According to its frequency replacement and function, the crusher parts are divided into crusher spare parts and crusher wear parts.
Crusher Parts Types
Different types of crusher, there are different crusher parts types.
Jaw Crusher Parts
A jaw crusher uses compressive force for breaking of particle. This mechanical pressure is achieved by the two jaws of the crusher of which one is fixed while the other reciprocates. A jaw or toggle crusher consists of a set of vertical jaws, one jaw is kept stationary and is called a fixed jaw while the other jaw called a swing jaw, moves back and forth relative to it, by a cam or pitman mechanism, acting like a class II lever or a nutcracker. The volume or cavity between the two jaws is called the crushing chamber. The movement of the swing jaw can be quite small since complete crushing is not performed in one stroke. The inertia required to crush the material is provided by a flywheel that moves a shaft creating an eccentric motion that causes the closing of the gap.
Based on its frequency replacement and function, the jaw crusher parts are divided into jaw crusher spare parts and jaw crusher wear parts.
Jaw crusher wear parts include:
- Fixed jaw plate
- Movable jaw plate
- Cheek Plate
Jaw crusher main spare parts include:
- Frames
- Eccentric shaft
- Bearings
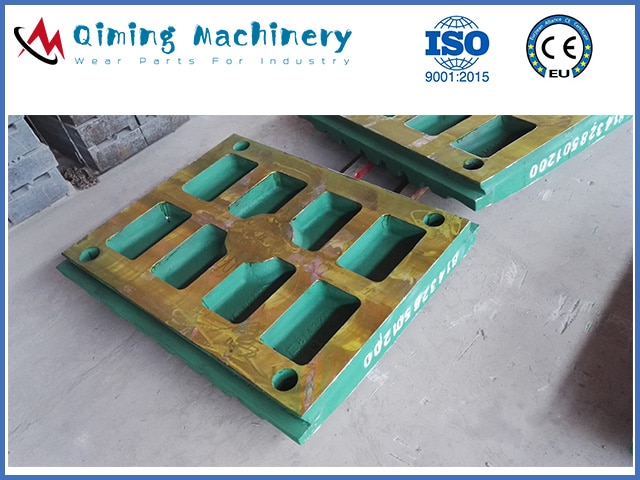
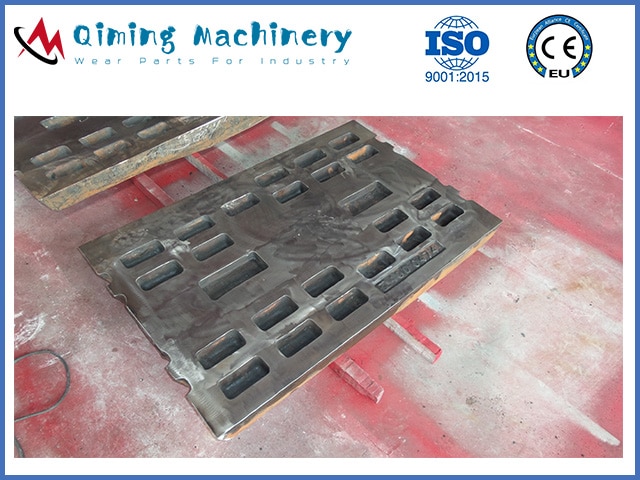
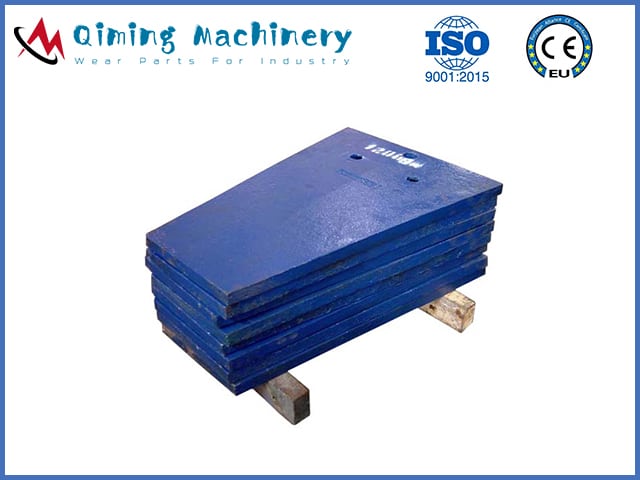
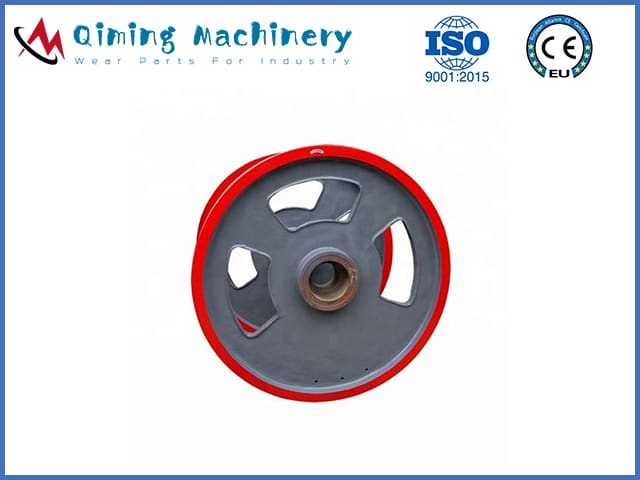
Cone Crusher Parts
A Cone Crusher is a compression type of machine that reduces material by squeezing or compressing the feed material between a moving piece of steel and a stationary piece of steel. Final sizing and reduction are determined by the closed side setting or the gap between the two crushing members at the lowest point. As the wedge or eccentric rotates to cause the compression within the chamber, the material gets smaller as it moves down through the wear liner as the opening in the cavity gets tighter. The crushed material is discharged at the bottom of the machine after they pass through the cavity.
Based on its frequency replacement and function, the cone crusher parts are divided into cone crusher spare parts and cone crusher wear parts. Details check the right standard cone crusher structure picture.
Common cone crusher wear parts include:
- Mantles
- Bowl liners
- Concaves
- Feed cones
- Mainframe liners
- Protection cones
- Armguards
Common cone crusher spare parts include:
- Frames
- Mainshaft
- Eccentrics
- Heads
- Bushings
- Pinions and gears
- Pinionshafts and countershafts
- Adjustment rings and bowls
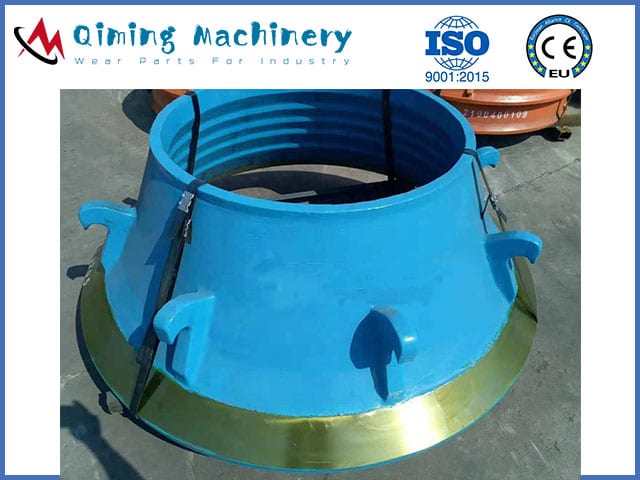
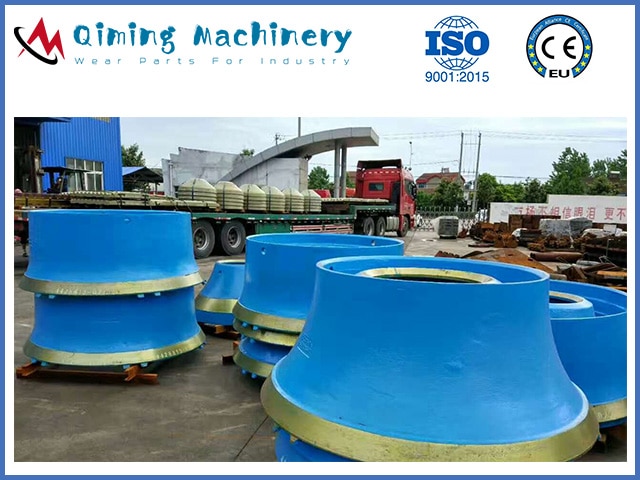
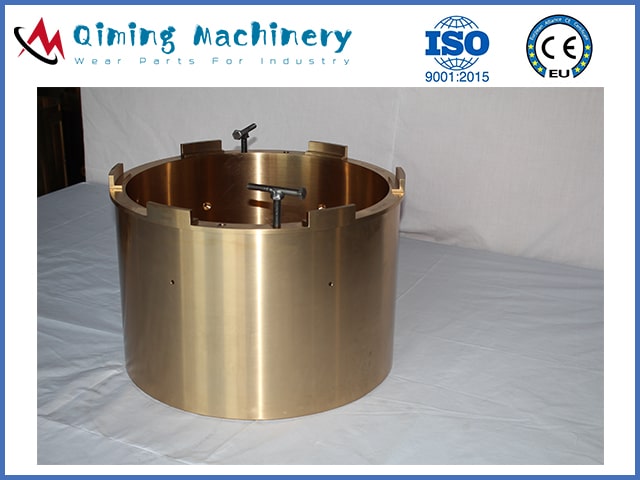
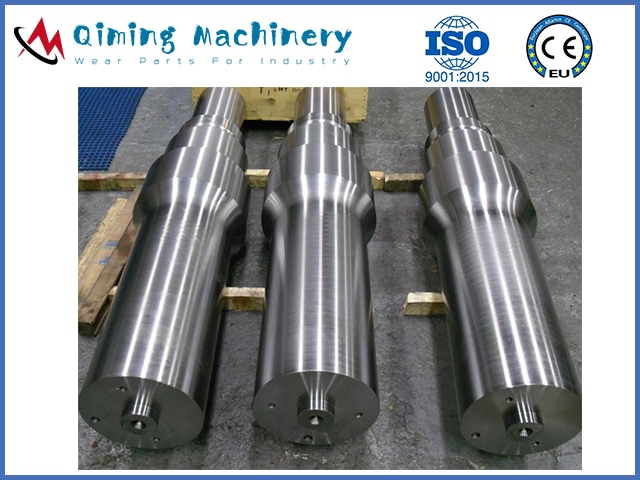
Gyratory Crusher Parts
A gyratory crusher includes a solid cone set on a revolving shaft and placed within a hollow body, which has conical or vertical sloping sides. Material is crushed when the crushing surfaces approach each other and the crushed products fall through the discharging opening. The gyratory crusher is similar in basic concept to a jaw crusher, consisting of a concave surface and a conical head; both surfaces are typically lined with manganese steel surfaces. The inner cone has a slight circular movement, but does not rotate; the movement is generated by an eccentric arrangement. As with the jaw crusher, material travels downward between the two surfaces being progressively crushed until it is small enough to fall out through the gap between the two surfaces.
Based on its frequency replacement and function, the gyratory crusher parts are divided into gyratory crusher spare parts and gyratory crusher wear parts. Details check the right standard gyratory crusher structure picture.
Common gyratory crusher wear parts include:
- Mantles
- Concave segments
- Bottom shell side liners
- Spider cap
- Arm liners
- Rim liners
Common gyratory crusher spare parts include:
- Shells and spider
- Mainshaft
- Eccentrics
- Spider bushing
- Bottom shell bushing
- Pinion and gear
- Step bearings
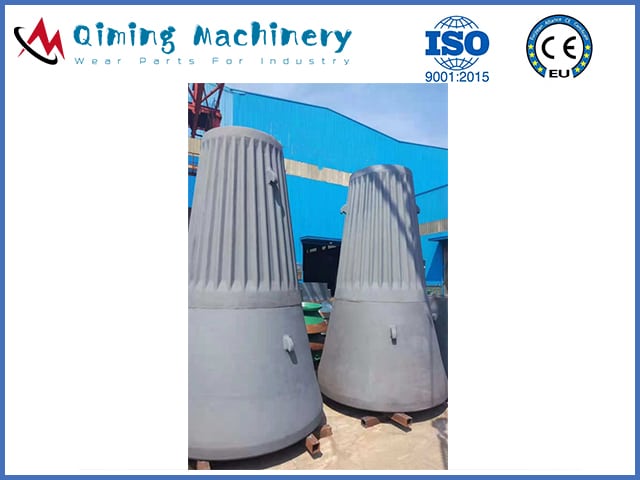
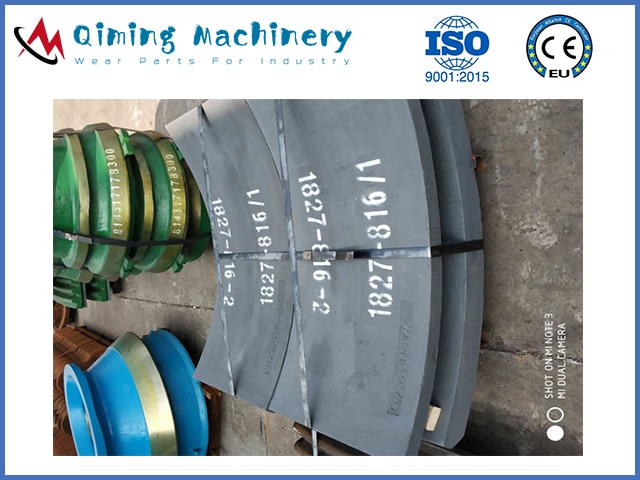
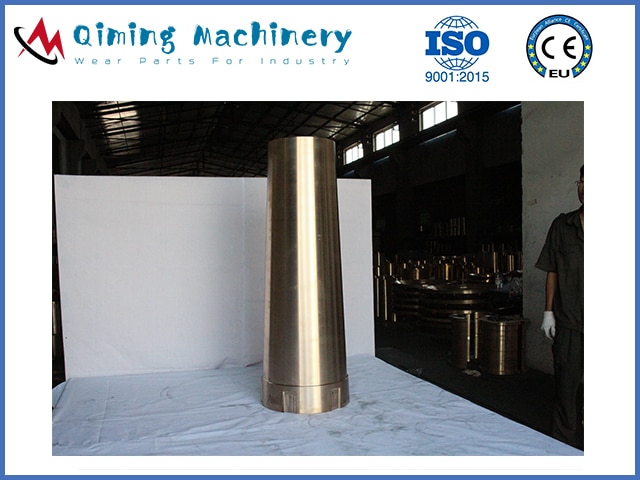
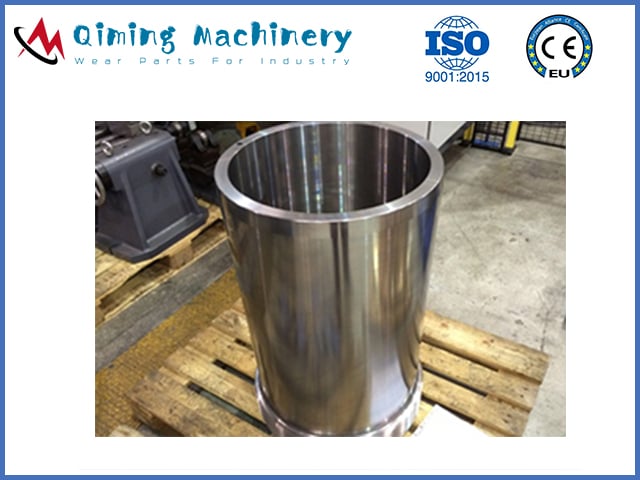
Impact Crusher Parts
Impact crushers involve the use of impact rather than pressure to crush material. The material is contained within a cage, with openings on the bottom, end, or side of the desired size to allow pulverized material to escape. There are two types of impact crushers: horizontal shaft impactor and vertical shaft impactor.
Vertical shaft impactor (VSI)
VSI crushers use a different approach involving a high-speed rotor with wear resistant tips and a crushing chamber designed to ‘throw’ the rock against. The VSI crushers utilize velocity rather than surface force as the predominant force to break the rock. In its natural state, rock has a jagged and uneven surface.
Common VSI wear parts include:
- Distributor plates
- Wear plates
- Anvils and shoes
- Rotor tips
- Breaker plates
- Feed cone
Common VSI spare parts include:
- Frames
- Rotor
Horizontal shaft impactor (HSI) / Hammermill
The HSI crushers break rock by impacting the rock with hammers that are fixed upon the outer edge of a spinning rotor. HSI machines are sold in Stationary, trailer mounted and crawler mounted configurations. HSI’s are used in recycling, hard rock, and soft materials. In earlier years the practical use of HSI crushers is limited to soft materials and non-abrasive materials, such as limestone, phosphate, gypsum, weathered shales, however, improvements in metallurgy have changed the application of these machines.
Common VSI wear parts include:
- Blow bars
- Impact plates
Common VSI spare parts include:
- Frames
- Rotor
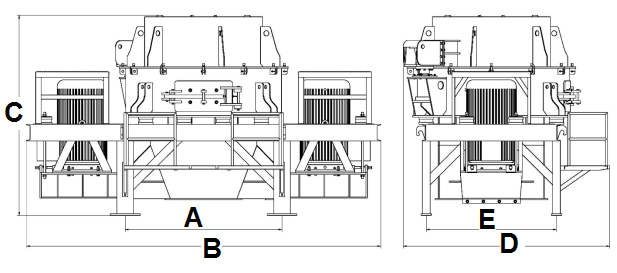
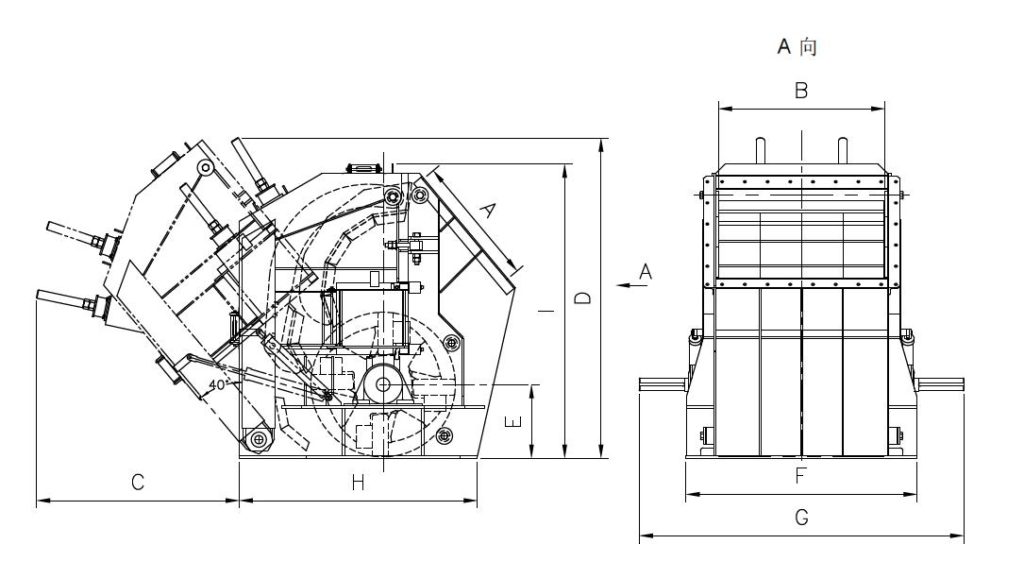
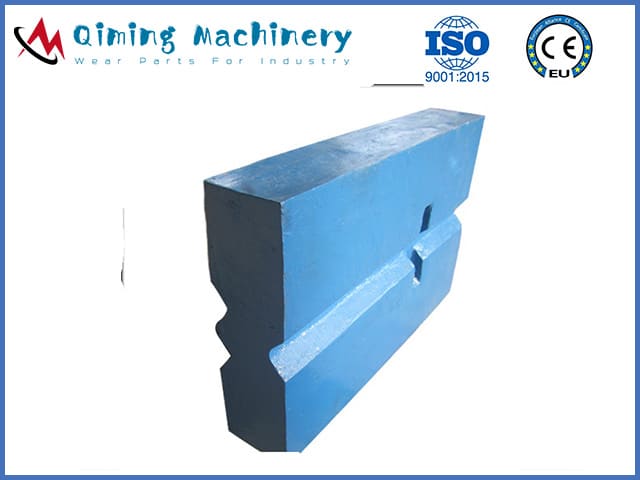
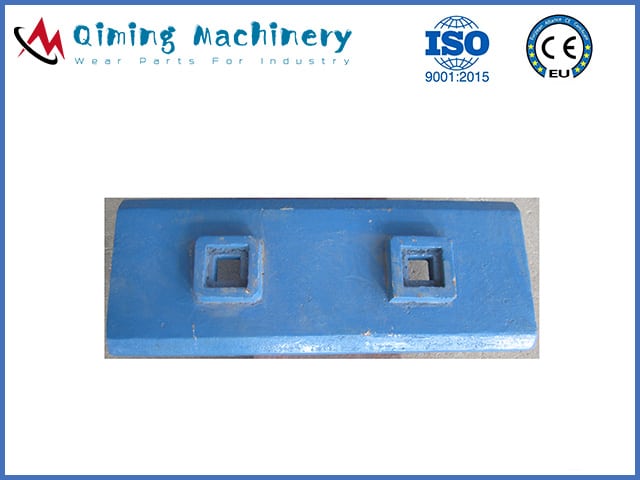
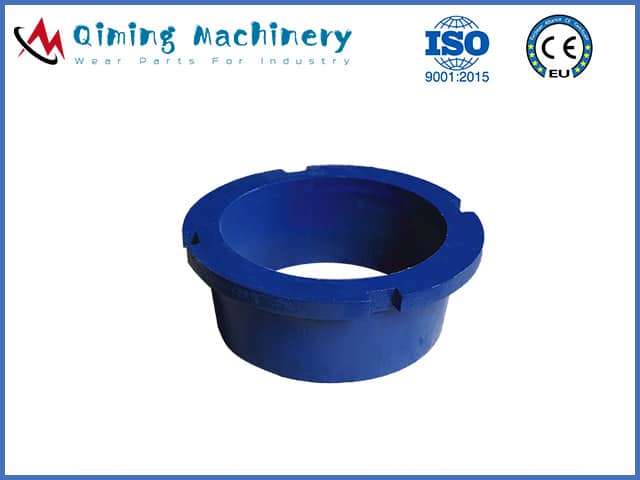
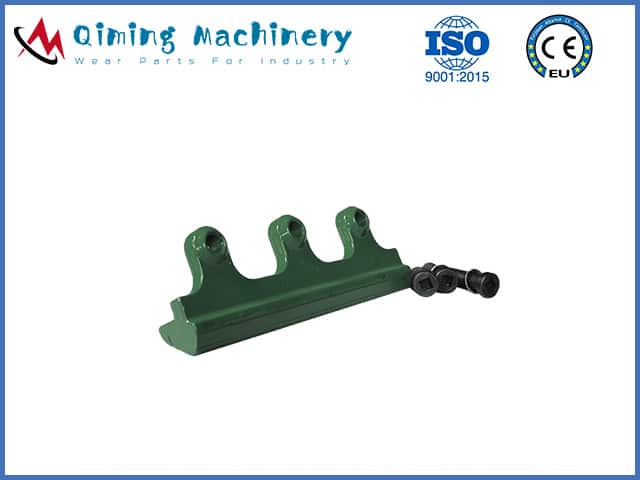
Main Crusher Parts Functions
For jaw crusher and their functions:
- Jaw plate. The members that perform the crushing and protect the pitman and frame from wear are commonly referred to as jaw dies. The jaw dies consist of a fixed and movable jaw plate.
- Pitman. The movable portion of the jaw crusher.
- Wedges. Devices that secure the jaw dies to the pitman and frame.
- Intermediate Plate. Fitting an intermediate (backing) plate behind the fixed jaw die reduces the nip angle of the crusher. The intermediate plate reduces the feed opening and the setting range by approximately the same amount as its thickness.
- Cheek Plates. Liners protect the sides of the frame in the crushing chamber.
- Toggle Plate. A release mechanism that will break or bend when tramp material is fed into the crusher. Connected to the bottom of the Pitman allowing it to move up and down.
- Protection Plate. Protection plates are designed for additional protection of the crusher’s frame and pitman due to erosion that can be caused by rubbing of the backside of the jaw dies. They are recommended when using small settings (always greater than or equal to the minimum recommended setting) and/or when the rock to be crushed is very hard (i.e.very low crushability). Of course, these can be used at any time for added protection. Some crushers come standard with the Protection Plates while others can be purchased as an option.
For Cone crusher and their functions:
- Cone crusher mantle. Covers the cone head of the crusher to protect it from wear. It is the inner sacrificial wear liner that sits on the cone head.
- Cone crusher concave. Sits in the upper frame of the crusher to protect it from wear. It is the outer sacrificial wear liner that sits inside the upper frame.
- Mantle nut. Used on the top of the mantle to secure the mantle in place on the cone head.
- Cone crusher main shaft. The main shaft is of high grade forged steel, annealed for stress relief. It is tapered to gauge for head center fit. The bottom of the shaft is fitted with a polished bronze step bearing.
- Head center. The main shaft is fitted with a steelhead center that bored and turned to gauge for shaft and mantle fit.
- Bottom shell. The annealed cast steel bottom shell is of the three arms, open discharge type, bored to gauge for the top shell, and eccentric bushing. It is boring and faced for the bottom plate, pinion shaft bearing, and dust collar.
- Main drive gears. The gears are straight tooth bevel gears and are designed to AGMA standards using a computerized program which, upon input of the basic information, such as DP, diameters, gear ratio, material properties, tooth type, provides a complete printout of the rated power on the basis of tooth strength and surface durability of the gear. The factor of safety on the gear is in excess of three on a strong basis and in excess of two on a durability basis.
For gyratory crusher and their functions
A gyratory crusher is made of six main assembly parts. Base, mainframe and concave liners, Drive assembly, mantle, spider arm assembly, and oil system.
- The Base. The base is the section of the crusher that provides an entry point for the drive assembly and oil system. It also provides support for the working surface of the mainframe and liners.
- Drive assembly. The drive assembly of a crusher may be directly driven from the MOTOR or have a system to absorb shock. This will depend upon the size of the equipment. If you remember, earlier in the session I stated that the RPM of a primary crusher was in the 100 to the 200 revolutions per minute range. The RPM of the Electric Motor driving the crusher will be higher than this. Normally to reduce this speed, pulleys or as they are technically called SHEAVES will be used. The sheave on the driveline of the crusher will be much larger than the one on the driveline of the motor. This means that the big sheave will travel much slower than the smaller ones on the motor does. By changing the SIZE RATIO between the crusher sheave and the motor sheave it possible to change the RPM of the crusher.
- Spider arm assembly. When you first look at the spider arm assembly it appears to only support the mantle. In reality, it has two other important functions to perform. The first to split the ore load as it enters the crusher, this helps in distributing the ore evenly over the crushing surface. The other function is to provide a protected passage for the lubrication lines that service the spider cap bearing.
- Concave segments. The concave liners’ main functions are protecting the crusher body and crush the stone or ore raw material. Most of the concave segments are designed to 3 layers and three-stage design.
- Gyratory crusher mantle. The mantle which is the movable working surface is pivoted at its top within a spider bearing under the cap of the spider arm assembly while the bottom is gyrated within an eccentric bushing which is powered by the drive assembly. For your better understanding let’s take a closer look at this system so you can see how this particular crushing action is generated.
- Oil system. Provides power and lubrication.
For HSI crusher and their functions:
- Rotor. This is the main part of the HSI crusher. It holds the blow bars and rotates at a high speed, being driven by a pulley connected directly to the engine.
- Blow bars/ Hammer. Wear parts inserted into the rotor which impact the rock to cause breakage. These can be replaced when they are worn down. There are two different options: (1). 4 high blow bars;(2). 2 high and 2 low blow bars. Some older design crushers had a 3 bar rotor.
- Aprons. Primary and Secondary aprons are used to reduce rock down to the required product size.
- Apron settings. This is the measurement the aprons are set at to achieve the product gradings. There are general rules of what the settings should be.
- Apron liners. Liners that are generally fitted to the end of aprons (which are replaceable wear parts) to
ensure the apron settings can be maintained. - Impact plates. Sometimes called frame liners, these are used on the inside of the impactor body to protect it from wear.
For VSI crusher and their functions:
- Rotor tips. The rotor tips function that it crushes the stones and ores.
- Back-up Tip. The back-up tip is designed to protect the rotor if and when a rotor tip gets broken or worn out. When this happens the Tungsten insert in the rotor tip has split and is now letting feed material run against the Tungsten insert of the back-up tip.
- Tip / Cavity Wear Plates. Tip / Cavity Wear plates are designed to protect the outside edges of the rotor against excited particles in the crushing chamber
- Upper and Lower Wear Plates. These wear plates are designed to protect the upper and lower faces of the inside of the rotor from the feed material as it passes through the rotor
- Distributor plate. The Distributor plate is designed to protect the plate that joins the Rotor, Rotor Boss and
Shaft together from feed material falling into the rotor from the hopper. - Trail plates. The Trail plates are designed to hold in the material build-up inside the rotor behind the rotor tips.
- Top and bottom wear plates. The Top and Bottom wear plate is designed to protect the top and bottom outside surfaces of the rotor
- Feed tube and feed eye-ring. The Feed tube and Feed eye ring are designed to guide the feed material into the rotor after it has been through the hopper.
Crusher Parts Price
If you need original OEM crusher parts, you can check with your crusher brand manufacturer or local part department agency. If you need aftermarket replacement crusher parts, the price can be the following.
Spare parts price
For some spare parts, such as hose, bolt, nuts, pins, seal, adapter, motor, and other spare parts, the price is based on per pcs or set. Those aftermarket replacement spare parts price around 40%-60% of the original parts.
Casting wear parts price
For casting wear parts, such as jaw plate, cone liner, blow bars, mantles, and other casting wear parts, the price is based on the casting material. For example, a set of jaw plate, weight:1000kg, material: Mn18Cr2.
The price USD2200 = Pattern fee(USD600, USD0.6 per kg for wood pattern) +Casting fee (USD1600, USD1.6 per kg for Mn18Cr2)
How To Choose The Right Crusher Parts And Suppliers?
Find the right crusher parts
All crusher plant have their part manuals. When you purchase the crusher, you can get the operation manual and part manual. Check in the manual book to find which part number crusher parts your inquiry.
If you need aftermarket crusher parts, you also can ask a professional engineer to measure the drawings or send a sample product to our suppliers.
Find the right suppliers
If end-users need the original OEM parts, just check with the original parts departments or local agency. If end-users need the aftermarket replacement parts and want to find the right aftermarket parts suppliers, the following things must be prepared:
- Know the part number
- Get the inquiry parts drawings
- Know the standard material for inquiry parts
- Know how to check the inquiry parts quality
Know the part number
The part numbers can find in the operation manual book. Some part numbers also cast in the part unwork surface.
Get the inquiry parts drawings
The drawings can purchase from drawings businessmen or ask a professional engineer to measure CAD drawings.
Know how to check the inquiry parts quality
For most of casting wear parts, check the quality by sizes report, material report, Mechanical behavior report, and flaw detection report.
Know the standard material for inquiry parts
There are some standard materials for common crusher wear parts.
For jaw crusher:
- Fixed jaw plate. Standard material is manganese steel which includes Mn14, Mn18, and Mn22.
- Movable jaw plate. Standard material is manganese steel which includes Mn14, Mn18, and Mn22.
- Flywheel. The standard material is carbon steel, which includes ZG250-700, ZG20SiMn,G20Mn5, ASTM A148, ASTM A488, ASTM A781, ASTM A802 etc
For cone crusher:
- Mantles and concaves. Standard material is manganese steel which includes Mn14, Mn18, and Mn22.
- Eccentric bushing. Standard material is High-Leaded Tin-Bronze.
- Frames and adjustment rings. The standard material is carbon steel, which includes ZG250-700, ZG20SiMn,G20Mn5, ASTM A148, ASTM A488, ASTM A781, ASTM A802 etc
For gyratory crusher:
- Gyratory mantles. The standard material is manganese steel which includes Mn14, Mn18, and Mn22.
- Concave segments. Upper and middle stage liner standard material is manganese steel (Mn14, Mn18, and Mn22), the bottom stage liners standard material is low alloy steel and high chrome steel.
For HSI crusher:
- Crusher blow bars. Standard material is high chrome steel (Cr27), based on crush material, the blow bars also manufactured by Manganese Steel, Chrome White Iron, Martensitic Alloy Steel, Chrome Iron + Ceramic Matrix, and Martensitic Alloy Steel + Ceramic Matrix.
- Impact crusher plate. The standard material is high chrome steel (Cr15).
- Apron and apron liner. The standard material is carbon steel, which includes ZG250-700, ZG20SiMn,G20Mn5, ASTM A148, ASTM A488, ASTM A781, ASTM A802 etc
For VSI crusher:
- Rotor tips. The standard material is Tungsten Carbide inserts alloy steel.
- Wear plates. Most of VSI crusher wear plates standard material is chrome steel.
Who is the crusher parts manufacturer?
Famous crusher parts suppliers In the world
There are thousands of crusher parts manufacturers in the world. The following companies are some quality manufacturers or suppliers.
- Columbia steel. It is the famous wear parts casting foundry, located in the USA.
- Flsmidth Inc. It is a crusher spare parts supplier, located in the USA.
- HE Parts. It is a crusher spare parts and wear parts supplier, located in Australia.
- ESCO Corporation. It is a crusher plant and parts supplier, located in Australia.
- CMS Cepcor. It is a crusher plant and parts supplier, located in the UK.
Quality crusher parts manufacturers in China
China is the biggest industry product manufactures in the world, there are some quality crusher parts manufactures:
- Mayang foundry. It is the most famous manganese steel casting foundry in China.
- JYS Casting. It is the fastest-growing wear-resistant materials casting foundry in China.
- Kinglong Group. It is the gear and pinion manufacturer who OEM for most pf famous crusher brands.
- Huafeng Industry. It is a carbon steel casting foundry, who supply frame and adjustment rings for crusher.
- MGS Casting. It is the oldest manganese steel and alloy steel casting foundry in China.