Jaw crusher is mainly used in mine production. Jaw crusher fixed jaw is a key jaw crusher spare parts in this series and belongs to the newly developed product series of our company. This product is a large-scale box-type steel casting, which is mainly produced by integral casting. There are many series of fixed jaw castings, and the casting process is similar, so here is only a series of fixed jaw technology solutions.
This jaw crusher fixed jaw material: ZG20Mn; Weight: 5.675t; Max Size:2294mm*1170mm*700mm; the average thickness 40mm. The product is complex in shape, see in the following picture. In addition, all inspections (magnetic powder and ultrasonic) are required, and the inspection level is DIN1690-V3, so it is difficult to manufacture.
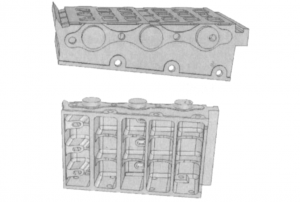
Jaw Crusher Fixed Jaw 3D Solid
Process plan
After careful analysis, consider the use requirements and technical requirements of castings, follow the principle of sequential solidification, and put forward the following process solutions in combination with our company’s previous production experience, as shown in the figure.
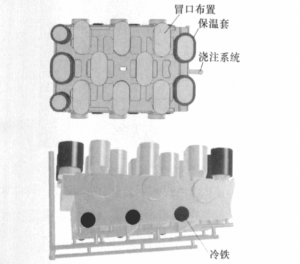
Jaw Crusher Fixed Jaw Process Plan
- The concave-convex platform is the upper surface for casting.
- Considering that most of the concave and convex flat surface of the casting is not processed, special risers are used when setting the riser to avoid the phenomenon of sand inclusion. At the same time, cold iron is placed at the three convex positions on the lower side of the casting.
- The bottom-injection pouring system is used in production, which can reduce the impact on the cavity, make the filling of the metal liquid more stable, and better ensure the internal quality of the casting.
- The overall shape is taken out of the actual wooden mold, and the inner cavity is made into 8 core boxes.
- Ester-hardened chromite ore sand is used for the exterior and core sand, and ester-hardened quartz sand is used for the intermediate sand, and limestone sand is used for the back sand.
Computer simulation
According to comprehensive considerations of various aspects, three-dimensional solid modeling is performed with reference to the above process scheme, and then computer numerical simulation is performed to simulate the solidification simulation and filling simulation of the casting.
Solidification simulation
After computer simulation process plan is determined, it is carried out by computer solidification simulation, as shown below:
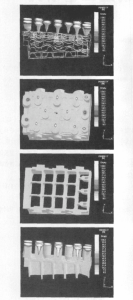
Solidification simulation
Judging from the results of solidification simulations, this process solution is feasible, there is no large shrinkage of the casting body, the internal quality is good, it can meet the technical requirements, and it can fully meet the flaw detection requirements after actual production verification.
Filling simulation
To further verify the rationality of the pouring system and the stability of the molten steel filling,computer simulation of the filling of the pouring system, as shown in the figure below:
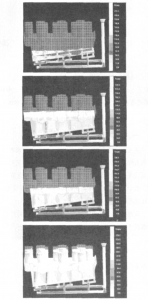
Filling simulation
From the filling simulation, it can be seen that the bottom-injection pouring system can minimize the impact on the cavity, ensure the size and shape of the cavity, and avoid trachoma defects caused by flushing the sand during the pouring process. At the same time, the pouring system It can also ensure that the molten steel rises smoothly, which is conducive to the slag and inclusions in the molten metal floating. The number of injectors can fully meet the rising speed of the molten steel, and better guarantee the internal quality of the casting! Avoid the occurrence of cold insulation.
Production results
Based on the simulation and demonstration of the process plan, the surface quality of the castings produced by the above plan is good, and there are no defects such as sand sticking and shrinkage, and the flaw detection is qualified once after roughing, which verifies the reliability of the simulation results. It can reach more than 75% and is now in mass production.