Qiming Machinery has 3 kinds of casting types to cast jaw crusher liner. Sand Casting casting type, V method casting type, and Lose Foam Casting casting type.
Jaw Crusher Liner Sand Casting
This casting type is the most popular in the casting area. Qiming Machinery also has rich experience in this. We use resin sand casting to cast jaw crusher liner.
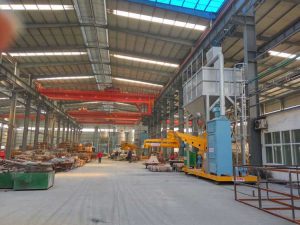
Jaw Crusher Liner Sand Casting
Casting Process
-
- Check the drawings and make a 3D model.
- Make a wood or steel pattern. In sand casting, the mold is made of wood or other metal materials. In this process, we asked our engineers to make the mold size slightly larger than the finished product, and the difference is called shrinkage margin. The purpose is that the molten metal acts on the mold to ensure that the molten metal solidifies and shrinks, thereby preventing voids during the casting process.
- Core making. The core is made by placing resin grit in the mold to form a casting on the inner surface. Therefore, the gap between the core and the mold eventually becomes casting parts.
- Forming. A set of molds need to be prepared during the smelting process. Forming usually involves supporting the mold frame, pulling the mold to separate it during the casting process, melting the previously placed core in the mold, and closing the mold mouth.
- Cleaning. The purpose of cleaning is to remove sand, sanding, and excess metal in castings. Welding and sand removal can improve the surface appearance of castings.
The burned sand and scale were demolished to improve the appearance of the casting surface. Excess metal and other risers are removed. One more step of welding and grinding. Finally, check its defects and comprehensive quality. - Heat Treatment.
- Machining
Jaw Crusher Liner V Method Casting
Both V method casting and lost foam casting use vacuum forming, but the process flow between the two is quite different. Vacuum process casting is named after the prefix “V” in English Vacuum (vacuum). It is different from the traditional sand casting. The biggest advantage is that no binder is used. The V method casting uses a plastic film to seal the sandbox, and the internal air is pumped out by the vacuum exhaust system. There is a pressure difference between the inside and outside of the casting mold, which makes the dry sand dense The required cavity is vacuumed through the lower core, the box, and pouring to solidify the casting and release the negative pressure, and the molding sand collapses to obtain the casting.
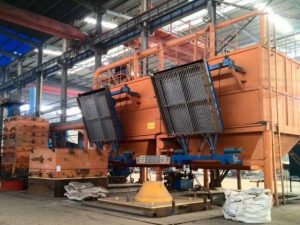
Jaw Crusher Liner V Method Casting
Casting Process
- The model puts the pattern on a hollow template with a large number of ventilation holes. When the vacuum is applied, these holes help to make the plastic film adhere to the pattern.
- Film heating. A plastic film with a large stretch rate and a high plastic deformation rate is heated and softened by a heater. The heating temperature is generally 80 ~ 120 ℃.
- Film-forming .Cover the softened film on the surface of the pattern, through the air hole, under the vacuum suction of 200 ~ 400mmHg, make the film adhere to the surface of the model.
- Sandbox. After spraying the paint and drying it (not required in the process), place the special sandbox on the model covered with film.
- Sanding and vibration. Add dry sand with better filling efficiency and particle size of 100-200 mesh into the sandbox, and then perform micro-vibration to make the sand compact to a higher density.
- Cover mould. Open the gate cup, scrape the surface of the sand layer, cover with plastic film to close the sandbox.
- Mold. The sandbox is evacuated to harden the mold under the action of atmospheric pressure by means of the film covered on the surface of the sandbox. When the mold is lifted, the vacuum of the negative pressure box is released to release the adsorption force of the template to the film, and then the top box is lifted to complete a mold.
- Box pouring. Before the box is combined, the core and cold iron can be lowered according to the process requirements, and the upper and lower boxes are combined to form a casting mold with a riser and a cavity, which is poured in a vacuum state.
- Unboxing. After an appropriate cooling time, the vacuum is canceled to restore the normal pressure state, so that the free-flowing sand flows out, and a clean casting without sand block and mechanical sticky sand is stored. The sand can be reused after cooling.
Jaw Crusher Liner Lost Foam Casting
Lost foam casting (also known as solid casting) is the combination of paraffin or foam model similar to the size and shape of the casting to form a model cluster. After being coated with refractory coating and dried, it is buried in dry quartz sand and vibrated. Under negative pressure Under casting, the model gasifies, liquid metal occupies the model position and a new casting method that forms the casting after solidification and cooling.
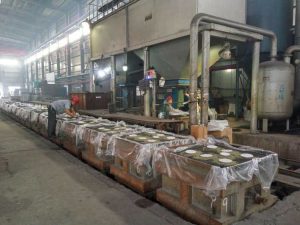
Jaw Crusher Liner Lost Foam Casting
Casting Process
1. Making foam gasification mold ;
2. Foaming gasification, drying after mold assembly;
3. Brush and spray refractory paint on the surface of the foam gasification mold and dry it again (must be completely dry);
4. Place the special sandbox on the three-dimensional vibration table;
5. Fill in the bottom sand (dry sand) to vibrate and level it;
6. Put the dried foamed gasification mold on the bottom sand, divide it into sand filling according to the process requirements, and scrape the box mouth after automatically vibrating for a certain time;
7. Cover the mouth of the sandbox with plastic film, put the gate cup, and connect to the negative pressure system. After compaction, the molten steel is cast, the foam gasification mold disappears, and the molten metal replaces its position;
8. After the casting is condensed, release the vacuum and turn over the box, take out the casting, and perform the next cycle.
Compare the three casting types in casting jaw crusher liner
- In order to decrease the pattern fee, most of the trail orders can use Lost Foam Casting.
- Lost Foam Casting can use cast less than 2000kg jaw plates. For more than 2000kg liner, Lost Foam Casting can not promise the sizes.
- V-method Casting use to cast standard jaw crusher liner, which can decrease the cost.
- Sand Casting jaw crusher liner surface finish not good as the others