Stone crushing machinery is widely used in many departments such as mines, smelting, building materials, highways, railways, water conservancy, and chemical industry. With the development of the world economy, the revival of mining and other basic industries, the demand and increasing of crushers, customers’ requirements for product quality and performance are becoming higher and higher. As an important large-scale casting in mining machinery, the main frame has a complex structure, small and uniform wall thickness compared with the upper bracket, upper bracket, and middle bracket. It is difficult to realize the sequence congealing of castings due to the structural characteristics. During the production, the defects of deformation, shrinkage porosity and shrinkage cavity are relatively prominent. After magnetic particle inspection, the magnetic marks beyond the standard show that it not only affects the quality of the product, increases the cost, but also affects the delivery time. In this paper, the numerical simulation technology of solidification process is used to optimize the casting process, ensure the sequential solidification of castings and the feeding effect of molten steel, finally solve the shrinkage cavity and shrinkage porosity defects of the main frame, improve the quality of the main frame, and ensure the batch stable supply of such products.
Basic parameters and technical requirements of cone crusher main frame
We just manufacture an MP800 cone crusher main frame for our customers, so we choose this part as an example.
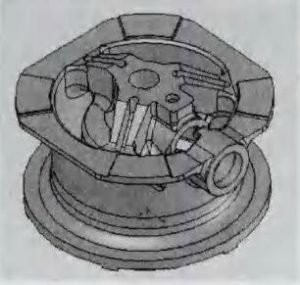
MP800 Cone Crusher Main Frame
The MP800 cone crusher main frame is very large, size: 3727*2436 (mm), weight:35.3t, material: J03006
J03006 Chemical Composition | |||||||
C | Si | Mn | S | P | Ni | Cr | Mo |
0.25-0.35 | 0.2-1.0 | 0.7-0.75 | ≤0.04 | ≤0.04 | ≤0.5 | ≤0.25 | ≤0.2 |
The production process of cone crusher main frame
1.According to the analysis of casting structure, the parting plan of casting is determined. The minimum wall thickness of the belt and the lower large flange are designed as parting surfaces, as shown in the following figure:
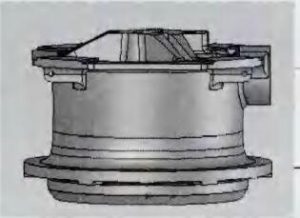
MP800 Cone Crusher Main Frame Parting Plan
2. The feeding way is designed according to the casting sequence solidification way. From the structural analysis, there are large hot spots at the upper and lower flanges, and it is difficult to realize the sequential solidification in the same direction. Therefore, the cold iron is designed from the middle belt, and the feeding riser is designed at the upper and lower flanges.
3. The bottom return pouring system is adopted for the pouring mode, that is, the liquid steel is led to the bottom of the casting through the sprue and cross sprue, and then injected into the mold cavity from the bottom by the inner gate.
Cone crusher main frame casting part problems and analysis
Cone Crusher Main Frame Casting Part Problems
In actual production, the initial process is used for modeling and pouring. A large amount of shrinkage was found at the belt, and the hardness of the casting at the intermediate shaft hole failed to meet the technical requirements, as shown in the figure:
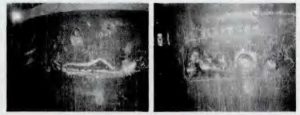
MP800 Cone Crusher Main Frame Problem
Analysis of Problems
In the process of casting cooling from pouring temperature to room temperature, there are three interrelated shrinkage stages: liquid shrinkage, solidification shrinkage, and solid shrinkage. According to the solidification theory, the volume shrinkage between liquid-solid phase lines is the main stage of forming shrinkage cavity and shrinkage porosity. Large and concentrated holes are called shrinkage cavities, while small and dispersed holes are called shrinkage cavities. When the liquid feeding channel is unobstructed and the dendrite does not form a network structure, the volume shrinkage shows a concentrated shrinkage cavity and is located in the upper part of the flowable unit of the casting; while when the dendrite forms a framework, the macro feeding channel is blocked, and the volume shrinkage of the liquid part surrounded by the dendrite partition shows a shrinkage porosity. Shrinkage porosity is a complex process, which is not only related to alloy properties and temperature but also related to the size characteristics of dendrites and their structural morphology, growth speed, external pressure and other factors
From the macroscopic point of view, it is considered that the wall thickness of the belt of mp800 main frame is relatively uniform, and the feeding riser of process design is set at the upper and lower flange processing surfaces. There is no metal subsidy at the casting belt, and a good wedge-shaped feeding channel is not formed, resulting in insufficient vertical finite feeding distance of the riser, and the casting wall center appears shrinkage during the solidification process.
From the view of solidification, the volume of molten steel begins to contract with the decrease of temperature after the pouring of main frame. When the casting is in the liquid state, there is no dendrite formation in the liquid metal, the feeding channel of the casting is unblocked, and the liquid metal has good fluidity. When the liquid shrinks, the molten steel in the riser can be fully fed. With the further decrease of temperature, the casting enters into the liquid-solid transition zone. At this time, the main solidification shrinkage occurs and the volume of liquid changes greatly. The feeding of casting mainly depends on three modes: mass feeding, dendrite feeding and explosive filling. At the later stage of solidification, a large number of dendrites began to form, with developed dendrites, connected dendrite arms, and a large number of network structures formed between dendrites. At this time, the dendrite arm is developed, which is not easy to be damaged by the liquid pressure difference. At the same time, the main frame structure here is the uniform wall thickness, and the solidification process occurs from top to bottom at the same time. A large number of dendrite connections hinder the feeding of riser liquid to this place, and “explosive filling” will not occur. The feeding fluid flows between dendrites with great resistance, which is basically seepage, so the fluid between dendrites can not get the external feeding and finally produce shrinkage porosity. From this point of view, the riser can not be increased in the subsequent process improvement.
The hardness of the casting at the shaft hole can not meet the technical requirements, mainly because the hardness of other parts of the piece is not high, only the hardness of this part is high.
Cone Crusher Main Frame Shrinkage Improvement
- The belt of mp800 main frame is too far away from the top riser, and the feeding gradient of riser is not enough. Through modulus calculation, increase the process allowance, increase the feeding channel, so that the feeding channel is later than the solidification of hot spot, so that the casting can achieve sequential solidification. After improvement, process allowance is added between riser and hot joint, so that shrinkage porosity can be avoided completely.
- Increase the effective feeding distance of riser. In general, the effective feeding distance of riser is L = R + e (ruler: feeding area of riser, e: end area). There are two ways to increase the feeding distance of the riser, i.e. to increase the riser place cold iron. However, in production, it is sometimes found that shrinkage occurs when the distance between the two risers is close to riser F. This is due to the thermal interference of the two risers and the prolongation of the solidification time. It is also possible that the two risers flow through each other and make the two risers and the riser solidify synchronously. In the later stage, shrinkage occurs when there is no feeding. Therefore, in the process modification, the cold iron is set between the upper and lower flange risers, and the cold iron is placed at the minimum wall thickness to increase the end area.
- Through local heat treatment, the hardness of the casting at this place can meet the technical requirements.
Through the improvement, Qiming Machinery had cast high-quality MP800 cone crusher main frame for our customers.