There are many reasons why your impact crusher blow bars are breaking on a regular basis. We have compiled a list of the most common causes of blow bar failure and the solutions to those problems.
Study Case 1
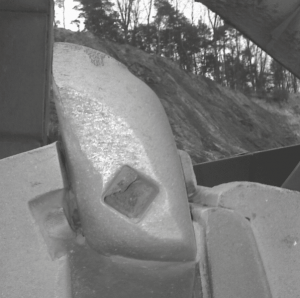
Excessive penetration on the blow bar
Problem: Excessive penetration on the blow bar
Causes:
- The rotor speed is too slow.
- Increases risk of blow bar breakage.
- The blow bar is under-utilized before changing.
- Increased rotor wear.
Solution:
- Increase the rotor speed.
- Change to 4 high blow bars.
Study Case 2
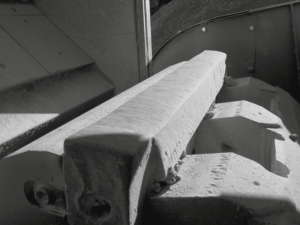
Poor penetration on the blow bar means the top of blow bars is worn down flat
Problem: Poor penetration on the blow bar means the top of blow bars is worn down flat.
Causes:
- The rotor speed is too high.
• Wear rates will be excessive.
• Reduced output.
• Creates a lot of fines
Solution:
- Reduce the rotor speed.
- Change configuration to 2 high and 2 low blow bars.
Study Case 3
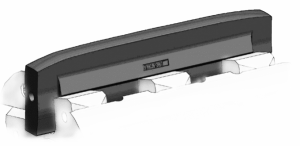
Wear on the sides of the blow bar
Problem: Wear on the sides of the blow bar
Causes:
- A high percentage of fines in the feed or overfeed causing fines to be pushed to outside.
- Crusher chamber contaminated with caked material causing friction wear.
Solution:
- Reduce speed of feeder so wear becomes even across the surface of the blow bar.
- Clean chamber daily after each shift.
Study Case 4
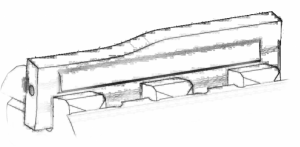
Blow bar wearing excessively to one side.
Problem: Blow bar wearing excessively to one side
Causes:
- The machine on uneven ground – material falling to one side
- The machine isn’t choke fed.
- Feed dropped onto one side of feeder when using a recirculating option.
Solution:
- Ensure the machine is on level ground.
- Continuous loading.
Study Case 5
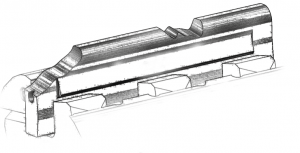
Blow bar is damaged or broken
Problem: Blow bar is damaged or broken.
Causes:
- Incorrect blow bar for an application. (E.g. Chrome)
- There is steel or rebar in the feed.
- The feed size is too large.
Solution:
- Select the correct blow bar.
- Control feed size.
- Remove steel or rebar.
Study Case 6
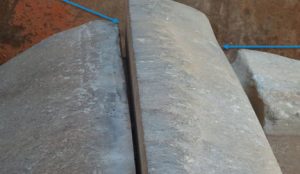
Blow Bar Not Seating Against Rotor
Problem: Blow Bar Not Seating Against Rotor
Causes:
- The rotor is not straight or needs to be rebuilt.
- Blow bar is not straight, defective, or not properly machined to specs.
- Blow bar could be pivoting, rocking on the locking mechanism, or there may be a fitting issue
Solution:
- Select the correct blow bar.
- Change the installation.
Study Case 7
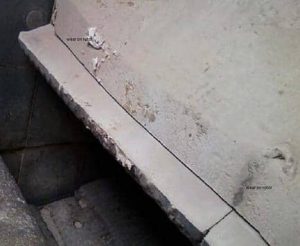
Worn and Cracked Rotor
Problem: Worn and Cracked Rotor
Causes:
- The rotor is not straight or needs to be rebuilt.
- Blow bars material not suit
Solution:
- Change to manganese blow bar.
- This rotor needs to be replaced or rebuilt.
Study Case 8
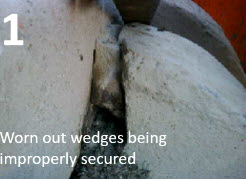
Lack of Blow Bar Support
Problem: Lack of Blow Bar Support
Causes:
- wedges not being used properly;
- user was forcing old nuts/bolts under wedges to push them up instead of jacking bolts/ set screws.
Solution:
- These wedges need to be replaced with new ones!
Study Case 9
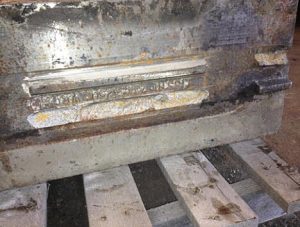
Loose Wedges
Problem:
The customer was experiencing breakage. When we went to the site, we found that the wedges were loose, causing the bar to move up in the rotor station, causing pressure on the locating nose. This pressure leads to a break in a blow bar. A new person was in charge of the crusher and did not realize they could loosen.
Solution:
A program was initiated to check wedge tightness a few hours after new blow bars were installed and at other intervals.