Wear is produced when two elements press against each other, such as an apron liner, blow bars, and crushing material. During this process, small materials from each element become detached, causing the surface to wear away. A primary factor in wear for crushing applications is abrasion. The blow bars on the rotor of an impact crusher wear faster because of the impact and rubbing with material during crushing. This contributes to about 60 % of the cost of wear parts in an impact crusher.
Which are influencing factors?
There are some factors that influence the wear of blow bars:
- Feed material
- Rotor speed
- Moisture content
- Fine content
- Crusher ratio
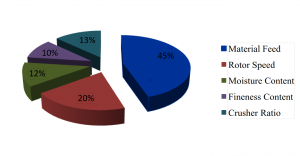
Blow bar wear factor considerations
There is a study that “Study of the wear behavior of limestone impact crusher blow bar”. Details check here: http://iosrjournals.org/iosr-jmce/papers/vol17-issue3/Series-3/B1703030512.pdf
This study shows:
After the above intervention, the length of the blow bar was measure after crushing 100,000 tons of limestone and 200,000 ton. The blow bars profile were observed and found to have worn uniformly at 0.000124 mm/ton on average at points A, B, C D, and E. Also, a gentle radius was observed on the blow bar. This shows the material fed into the crusher is the correct size; the rotor penetration and speed are correct, the correct blow bar for the feed material is being used and the machine parameter is correctly set up.
The wear rate of the rotor blow bar was optimized by ensuring that the material fed into the crusher is the correct size, rotor penetration and speed is correct, correct blow bar for the feed material is being used and machine parameter (such as gap setting) is correctly set up. This established that any deviation from the wear parameter impact significantly on the wear rate and maintenance cost.